AEGIS – Heavy-Duty Rotary Energy Exchanger
Designed for applications where extra strength in Casing and Rotor is required.
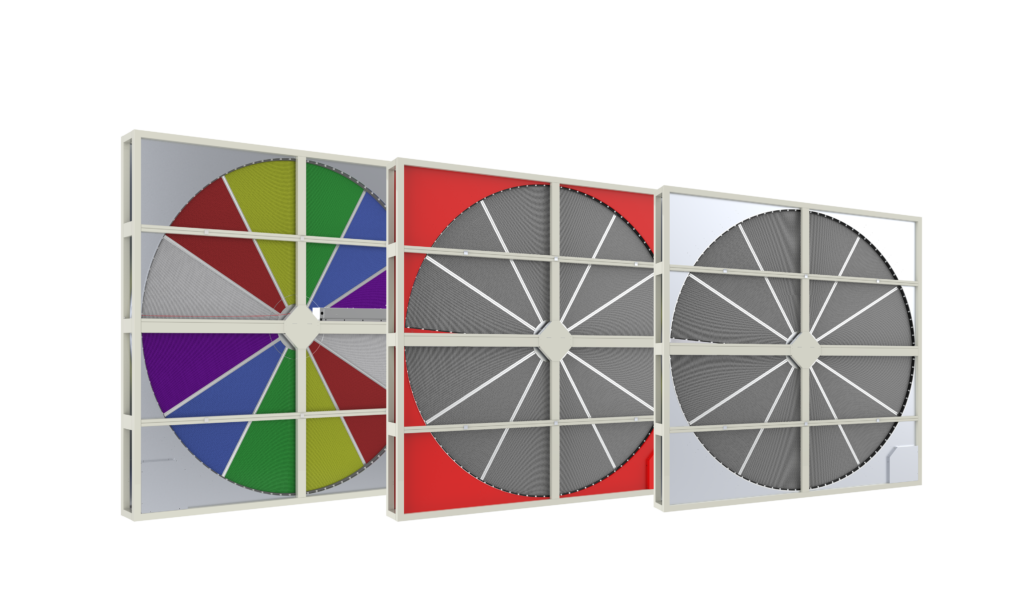
Designed for Heavy-Duty applications where normal units available on the market isn’t enough. Where extra strength is requested in both Casing and rotor, AEGIS is the best choice.
Designed for easy maintenance of bearing and drive unit.
Designed to support economic shipping on Sea and roads, and easy assembling on site.
Engineering and precision in every detail.
5- Years Limited Warranty as option.
■ Rotor
● Media in high quality aluminum alloy permanently coated with 3Å molecular sieve desiccants.
● Rotor divided into 12 segments.
● HUB (center) fully CNC- manufactured for perfection in every detail.
● External Bearing holder eXtreme with SKF bearing 2212-2RS. (optional: distance lubrication of bearing)
● Heavy Duty Radial-wall system.
● Individual CNC- connections of Radial walls for perfect alignment.
■ Casing
● Manufactured in welded tubular frame in 80x80x3mm.
● Divided horizontally into 4 pcs for easy assembling and shipping.
● Powder coated for high corrosion protection.
■ Drive unit
● High Quality Drive motor.
● Gearbox eXtreme with double radial sealing on outgoing shaft.
● 2 x A profile drive belt.
● Soft start.
AEGIS – HUB
The HUB is the central part of the rotor, all parts are therefore CNC- machined. It’s a solid ø250 mm steel HUB with Keyway for a ø70 mm Key-seated shaft. The seats for the Radial Wall attachment system are CNC-milled flat for a correct attachment of the Radial-wall anchors.
The external bearing holder eXtreme simplify the replacements of bearing while the rotor remains in the casing (without removal of rotor segments).
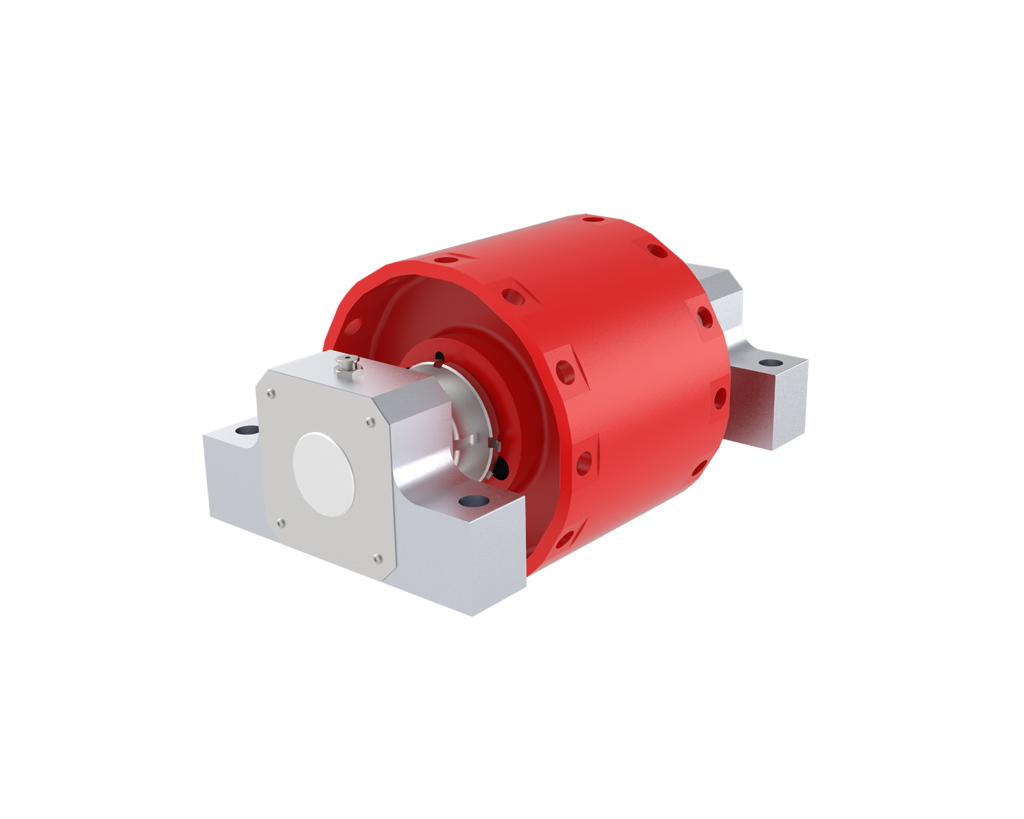
AEGIS – RADIAL WALL
The Radial wall system provides an extra rigid assembling of the rotor segments, the CNC- machined radial wall anchors, with fine machine threads gives a perfect base for precision alignment.
The steel periphery band divided in 12 pcs provides and extended tightening of the rotor segments.
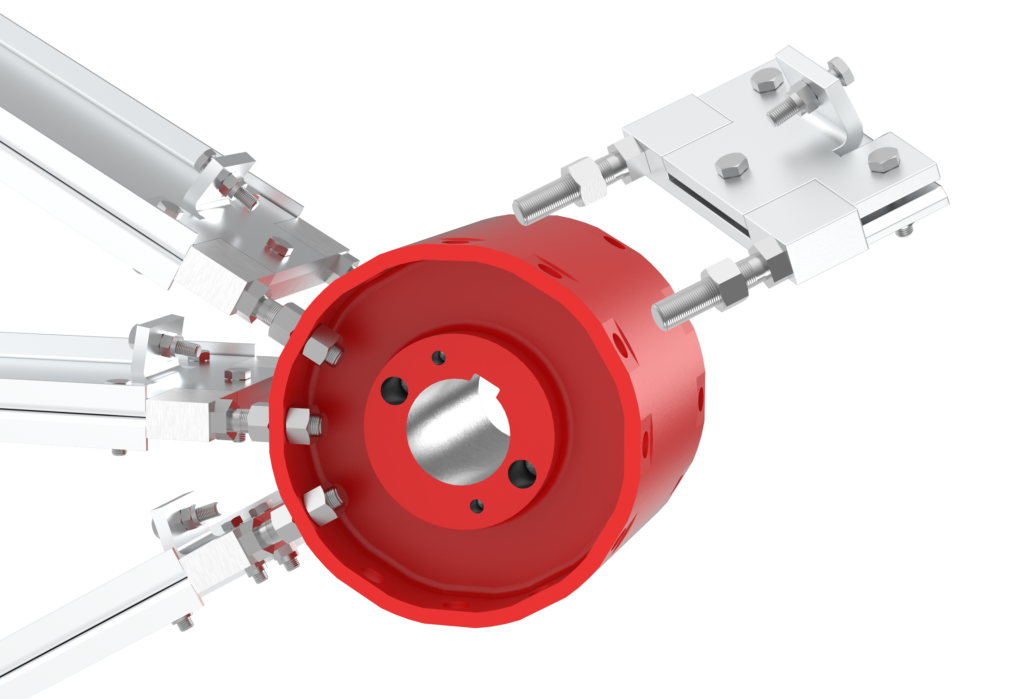
AEGIS – MEDIA
High quality aluminum permanently, fully coated with 3Å molecular sieve desiccants. The rotor surface is edge-reinforced for strengthening of the rotor surface and providing addition corrosion protection.
The high quality, high performing, light weighted media, reduces stress on the rotor and contribute to a reduced pressure drop over the rotor. Performance verified by AHRI and EUROVENT.
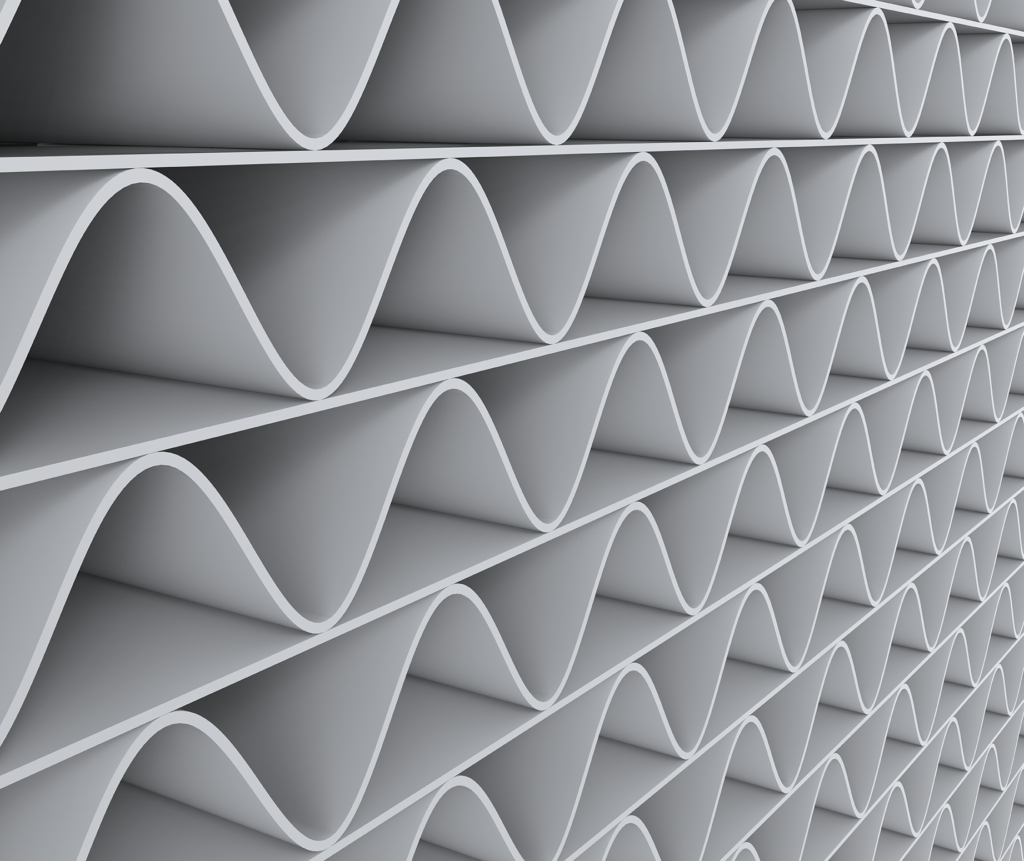
MEDIA
Ostberg’s OM- is a high-quality aluminum alloy, permanently coated with 3Å molecular sieve desiccants before the aluminum is shaped into a honeycomb media. The 3Å molecular sieve desiccants has one of the highest recovery performances of total energy in the business, at the same time it provides excellent corrosion protection. The edge- reinforcement applied in the final operation in the rotor production gives the media extensive protection from corrosion.
AEGIS – CASING
To avoid deflection the frame is fully welded in steel tubular 80x80x3 mm, the tubular middle beam of 120x60x3 mm gives extra strength. The casing is horizontally divided in 4 pcs with a go-through centralized 120x60x3mm vertical tubular support leg.
Powder coated for high corrosion protection. The casing can also be provided in stand-alone version, where a base frame, insulated panels and service doors are provided.
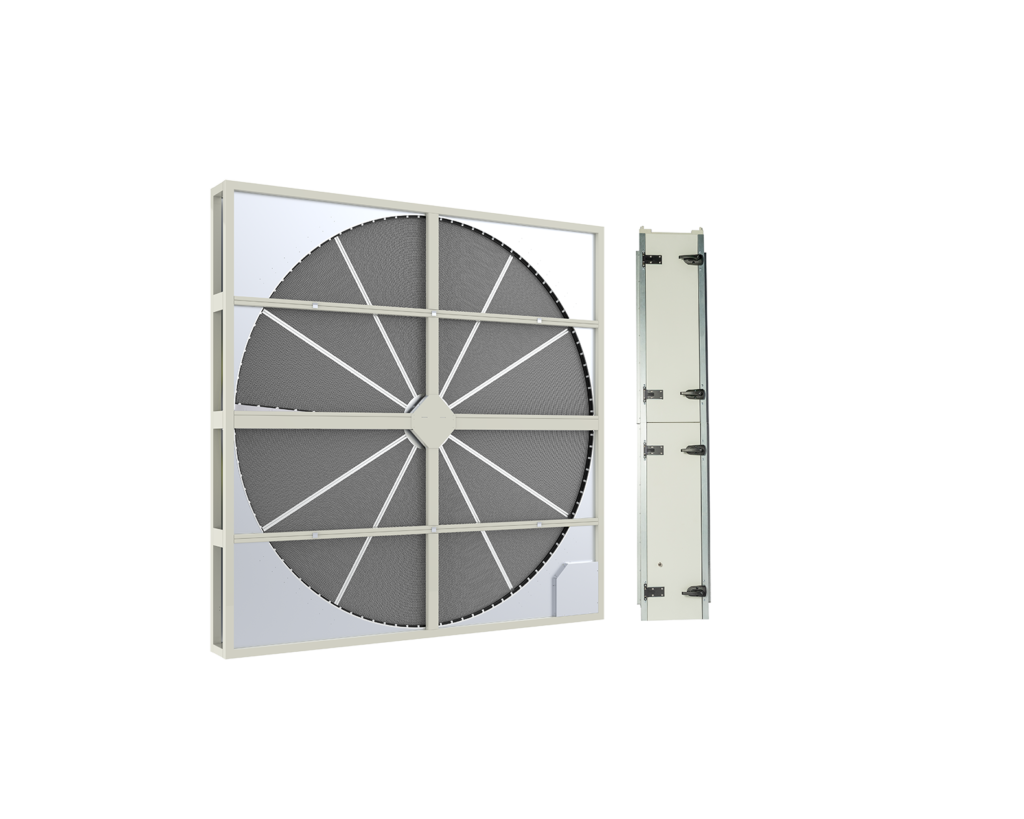
CASING
The casing is equipped with adjustable purge sector. The center of the casing design supports replacement of bearings / bearing holders without removing the rotor or segments from the casing.
AEGIS – Drive Unit
The drive system is design for long term operation with a minimum of maintenance. The gear box is provided with 2-layer of radial seals. 2 x standard A V-belt is used for an improved friction between pulley and drive belt, the drive belt rides on the “groove” that the special periphery plates create.
To minimize wear and tear on drive unit and drive belt, Soft-Start is provided as standard.
Improved service space around the drive motor is achieved due to expanded side panels.
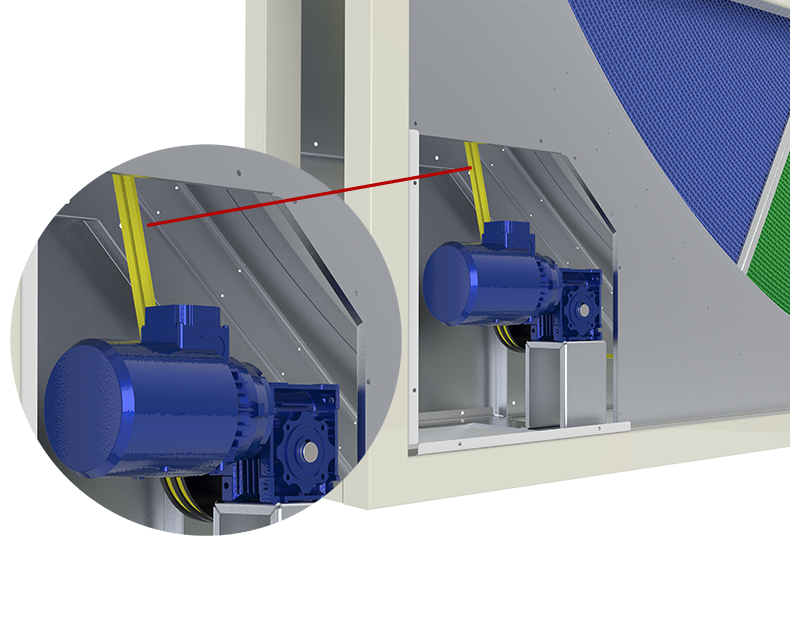
AEGIS – Sealing
Twin Sealing system is a combination of labyrinth function and brush sealing. By the fixed sealing channels created on the middle beam between the rotor surface and the middle beam a labyrinth function is achieved, the combination with the most used brush sealing system on the market the Twin sealing system provides a perfect sealing system.
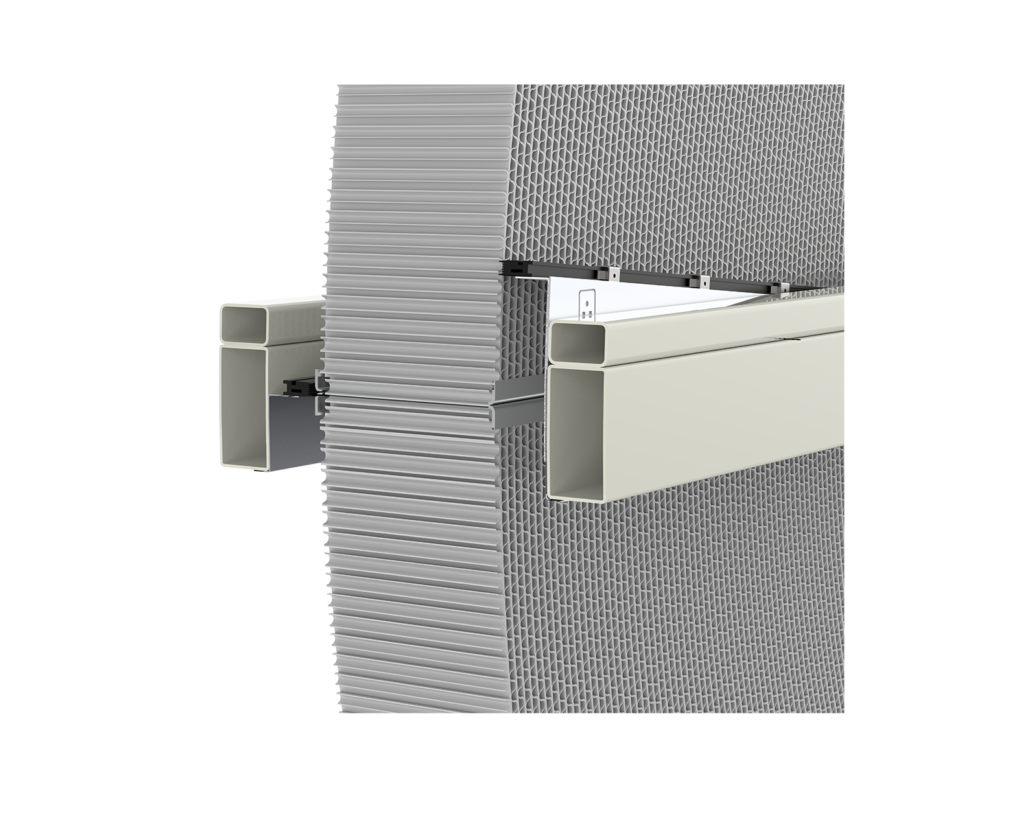